Automotive
Building automobiles of the future: Localization of EV supply chain in India
14 Aug 2020
India is the 4th largest passenger vehicle market
after China, USA and Japan. It is also the largest 2W and 3W market. Therefore,
India will play a pivotal role in the quest for EVs in the changing global
order. The opportunity to drive EV adoption will provide immense opportunities
for EV companies and component manufacturers in India.
Change in policies and
push for localization
Indian Government has created momentum for EVs
through its INR 10K Cr FAME Faster Adoption and Manufacturing of (Hybrid &)
Electric Vehicles Scheme. Under FAME-I, the Government aimed to make EVs
attractive largely by providing direct subsidies to customers and providing tax
cuts and reducing import duties for manufacturers, but it has tweaked the
policy under FAME-II where the emphasis has shifted towards building a robust
indigenous EV ecosystem.
FAME-II scheme placed additional restrictions
on EVs to be eligible for subsidies. OEMs now have to ensure at least 40%
localization (at ex-factory prices) for buses and 50% localization for other
categories. Benefits were discontinued for lead-acid batteries and were limited
to Li-ion batteries. Additionally, import duties on Completely Built Units (CBUs),
Semi Knocked Downs (SKDs), and Completely Knocked Downs (CKDs) were increased
by 5% to 25% w.e.f. April 2020. On the other hand, duties on Li-ion cells and
battery packs are set to increase from 5% currently to 10% and 15%. It will be
prudent to provide large scale incentives to develop giga-factories in India
before moving to a high tax regime on Li-ion cells, so India can develop the
required ecosystem to manufacture them.
Under the Phased Manufacturing Program (PMP)
which falls under FAME-II, the Government has already mandated indigenization
parts like HVAC (Heating, Ventilation, and Air Cooling), wheel rim integrated
with hub motor from October 2019 and other key components such as electronic
throttle, vehicle control unit, electric compressor, etc. by October 2021.
Several states in India are racing to attract
investments from OEMs and components players to emerge as an EV manufacturing
hub. Incentives range from setting up EV manufacturing parks, providing aid for
R&D and IP, partial or full reimbursements on land costs, financial
assistance on capital incentives, etc.
Opportunities and
challenges in EV localization
India’s vision to emerge as a major manufacturing hub for EVs
represents huge opportunities for the auto sector. While historically India has
been very good at cost engineering, there are challenges to be overcome to
realize this vision. Current levels of localization
in the Indian EV sector are as low as 20%
which has been limited due to the cost competitiveness of foreign providers,
deep technological expertise involved as well as limited access to crucial raw
materials such as lithium and rare earth magnets.
EV manufacturing requires deeper technological expertise than
ICE automobiles. In terms of cost, the battery is the most intensive component
of an EV contributing around 24% - 28% while BMS and TMS (Battery / Thermal
Management Systems) contribute an additional 10% - 14%. Other specialized parts
such as motors (10%), controllers (8%), and rest of drivetrain (7%) contribute
25% of the overall cost. The extent of localization going forward is not
expected to be uniform across components due to specific challenges in terms of
technology, raw materials, and the scale required to justify localization.
Several large players have invested US$ 1.5B in total
during 2019 - 2020 to set Li-ion battery manufacturing plants. Most
investments are concentrated in the state of Gujarat followed by Andhra Pradesh
and Telangana. However, widespread indigenization of Li-ion battery production
is unlikely in the medium to long term. Li-ion battery imports tripled from US$
348M in FY17 to US$ 1.2B in FY19, 85% of which was from China followed by
9% from Vietnam. We did detailed modeling of value chain localization based
on our EV Manufacturing Sophistication Model. By FY25, we estimate the
localization of Li-ion batteries in EVs to be 40% in the optimistic scenario
and 10% in the pessimistic scenario.
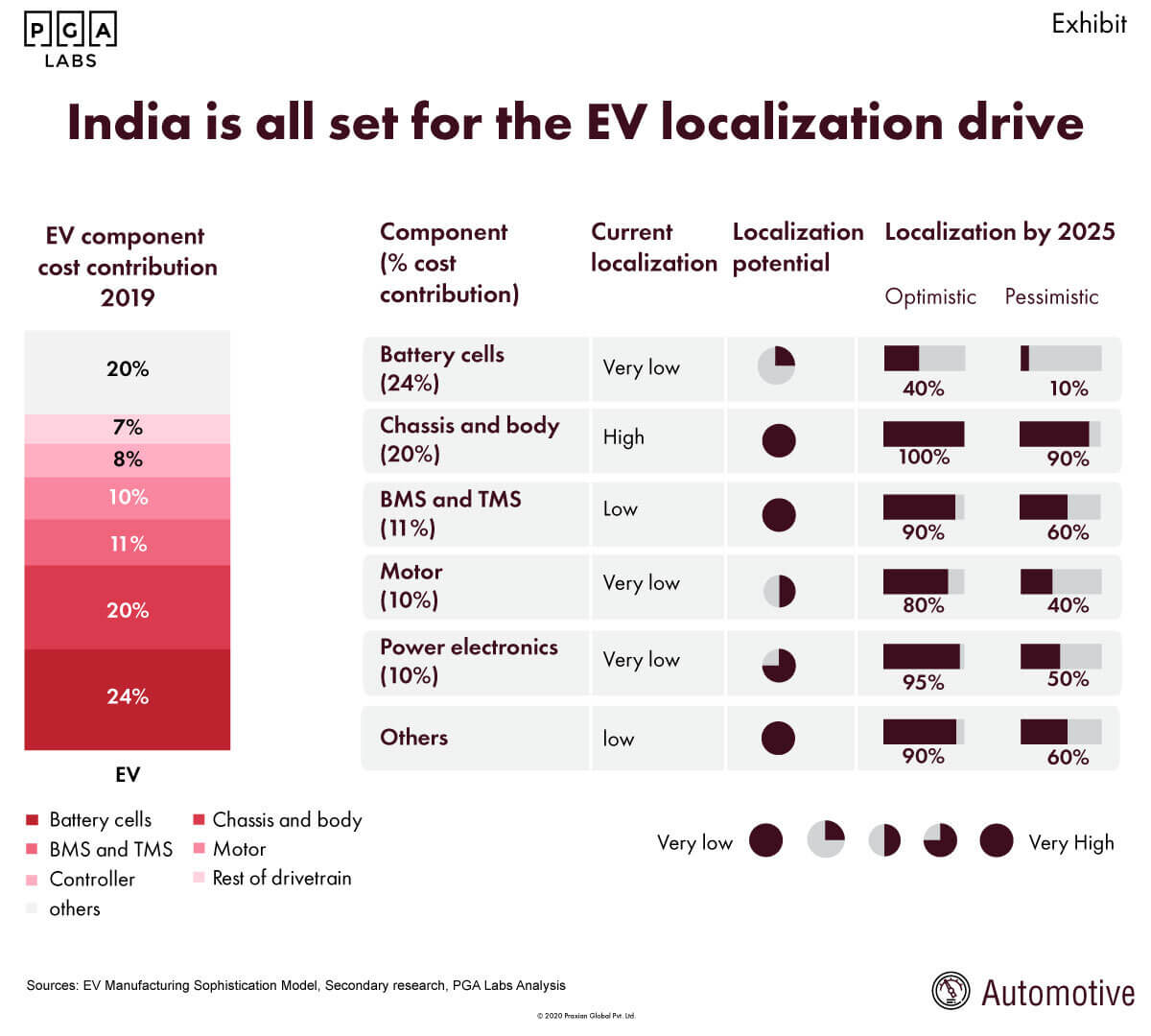
The above
exhibit shows that the contribution of batteries to EV cost is the largest.
Also, the potential for localization of chassis and bodies and BMS is high while
localization of specialized components such as batteries and motors could be
limited. Reasons for the current battery localization scenario include:
- Battery cells (24%): Lack of access to core raw materials like lithium and technology-intensive manufacturing to limit localization. Govt. needs to incentivize companies to acquire overseas Lithium mines
- Chassis and body (20%): These parts do not require special raw materials or technology and are already produced locally
- BMS and TMS (11%): Battery Management System technology is mostly software system driven and can be mastered locally
- Motor (10%): Lack of availability to rare earth magnets is a major hurdle. Large motors could take longer to localize
- Power electronics (10%): Power electronics like controllers and power IC are technology-intensive; capital investment necessary
- Others: Indian manufacturers are strongly positioned in this category which includes HVAC, control units, etc.
There are several major challenges to domestic Li-ion battery
production. Firstly, battery technology is currently evolving at a rapid pace
with new chemistries gaining popularity. The associated R&D is technologically intensive. Although the Indian Space
Research Organisation (ISRO) has transferred Li-ion battery technology to 10
firms that have set up plants in the country, India has not been at the
forefront of the innovations in battery technology.
The second major challenge is the unavailability of core raw material in the manufacturing of Li-ion
batteries, i.e. Lithium metal. India currently imports all its Lithium needs.
There is not comprehensive estimate available for Lithium reserves in India. In
Feb 2020, researchers at the Atomic Minerals Directorate, a unit of India’s
energy commission discovered around 14K tonnes of lithium reserves near Bengaluru
which is still very small compared to the leading countries. Chile has around
8.6M tonnes, Australia has 2.8M tonnes, Argentina has 1.7M tonnes and China has
1M tonnes of lithium reserves. In terms of production, Australia is the leader
with a production of 51K tonnes per year followed by Chile at 16K tonnes and
China at 8K tonnes.
The third major challenge is the cost competitiveness of Chinese Li-ion batteries. As in the case of
solar panels, China has ensured the global domination of Li-ion batteries.
China is home to 73% of the total installed capacity of Li-ion batteries
followed by the US far behind at 12%. Given the uncertainty around the exact
scale of EV adoption in India, large scale indigenization of batteries is
expected to take more time especially in case of large batteries (Passenger
vehicles, Commercial vehicles, buses, etc.).
The localization in
BMS and TMS can be high as they can be mastered in India relatively easily.
India is one of the leading exporters of software technology in the world.
According to RBI data, India’s software exports increased by 11.6% YoY and
amounted to US$ 108B in 2018. Field experience is critical for fine-tuning BMS
and that will come with a learning curve of the market, enhanced by sharing of
data from global leaders in the BMS space.
The unavailability of
rare earth magnets such as the Neodymium magnet which is the most widely
used in the production of motors for an electric vehicle is the key bottleneck
for the domestic EV motor industry. China is the leading producer of rare earth
magnets accounting for over 90% production and over 40% reserves. Small motors
for light electric vehicles would be relatively easier to manufacture locally,
but large motors need sophisticated technologies and could take longer to
localize. There have been advances in the field to reduce dependence on rare
earth magnets which can increase localization. E.g. Fraunhofer, a German
research organization discovered ways to reduce dependence on rare earth
magnets by up to 80%, however, the methods were not economical to scale. In
2018, Toyota managed to cut dependence on rare earth magnets by 20% in their
EVs. Localization of EV motors can reach up to 70% in the optimistic scenario
by FY25.
Power electronics,which include controllers, power IC's, etc. can be localized but are technology-intensive and would require investments in technology to be produced locally. There are already companies focusing on EV controllers, especially for the 2W and 3W markets where the incumbents are not strong, and a large opportunity exists. Global players are more focussed on PV and CV segments.
The winners in the EV supply chain will act decisively and fast to
make the automobiles of the future. To leverage India’s cost advantage and
achieve the desired high levels of localization of EV manufacturing in India,
ecosystem stakeholders need to start with the following:
- Commitment and investments in technology from incumbent OEMs and auto component companies
- Extensive focus on R&D would have to be facilitated to find alternatives and reduce dependence on scarce natural resources required for EV manufacturing
- Policymakers will have to strike a balance between promoting localization while making EVs economical & scaling charging infra to drive adoption and unlock economies of scale
Authored by:
Sanjeev Garg, Practice
Leader, Automotive
Aryaman Tandon,
Practice Director, Automotive